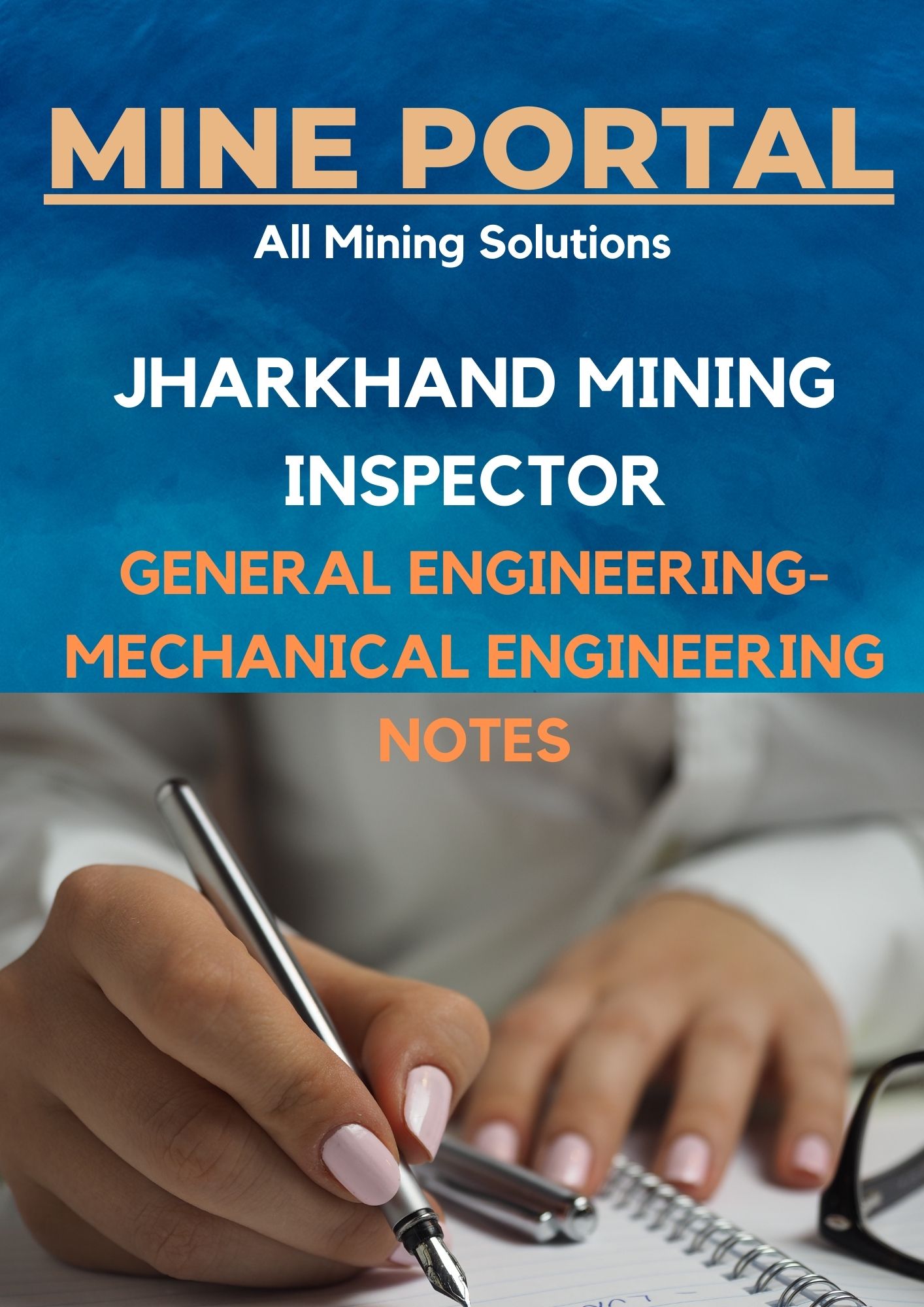
GENERAL ENGINEERING-MECHANICAL ENGINEERING NOTES
JHARKHAND MINING INSPECTOR GENERAL ENGINEERING-MECHANICAL ENGINEERING NOTES
Theory of Machines and Machine Design
Concept of simple machine, Four bar linkage and link motion, Flywheels and fluctuation of energy, Power transmission by belts – V-belts and Flat belts, Clutches – Plate and Conical clutch, Gears – Type of gears, gear profile and gear ratio calculation, Governors – Principles and classification, Riveted joint, Cams, Bearings, Friction in collars and pivots.
Concept of simple machine
A simple machine is a mechanical device that changes the direction or magnitude of a force. In general terms, they are defined as simple mechanisms that use leverage or mechanical advantage to multiply force. Simple machines have few or no moving parts to modify motion and force. They are the building blocks of more complex machines and are still widely used in industry and everyday life.
There are six main types of simple machines:
â—Lever :A bar or board that rests on a support called a fulcrum. A downward force exerted on one end of the lever can be transferred and increased in an upward direction at the other end, allowing a small force to lift a heavy weight.
â—Pulley :A wheel that rotates a rope, cord, or belt. It is used to change the direction of the force. By attaching a hook to the cord, the wheel’s rotation can be used to raise or lower objects, making work easier.
â—Inclined plane :A sloping surface that is used for raising heavy bodies. The plane offers a mechanical advantage in that the force required to move an object up the incline is less than the weight being raised (discounting friction). The steeper the slope, or incline, the more nearly the required force approaches the actual weight.
â—Wedge :An object that tapers to a thin edge. Pushing the wedge in one direction creates a force in a sideways direction. It is usually made of metal or wood and is used for splitting, lifting, or tightening.
â—Wheel and axle :A variation of the lever that can be used to move objects across distances. The wheel (round ends) turns with the axle (or cylindrical post), causing movement. The wheel and axle greatly reduce the friction involved in moving an object.
â—Screw :An inclined plane wrapped around a cylinder or cone. It converts rotational motion into linear motion. It is used to hold objects together or to lift or lower objects.
Four bar linkage and link motion
A four bar linkage is the simplest closed-chain movable linkage. It consists of four bodies, called bars or links, connected in a loop by four joints. Generally, the joints are configured so the links move in parallel planes, and the assembly is called a planar four-bar linkage. Spherical and spatial four-bar linkages also exist and are used in practice.
A joint may be either a revolute joint – also known as a pin joint or hinged joint – denoted by R, or a prismatic joint – also known as a sliding pair – denoted by P. A link that is fixed in place relative to the viewer is called a ground link. A link connecting to the ground by a revolute joint that can perform a complete revolution is called a crank link. A link connecting to the ground by a revolute joint that cannot perform a complete revolution is called a rocker link. A link connecting to a ground line by a prismatic joint is called a slider. A link connecting to two other links is called a floating link or coupler.
A four-bar linkage can be used for many mechanical purposes, including to:
â— convert rotational motion to reciprocating motion (e.g., pumpjack examples below)
â— convert reciprocating motion to rotational motion (e.g., bicycle examples below)
â— constrain motion (e.g., knee joint and suspension examples below)
â— magnify force (e.g., parrotfish jaw examples below)
The motion of a four-bar linkage depends on the lengths of its links and their relative positions. Grashof's theorem describes the conditions for a four bar linkage to have a unique and complete motion. The theorem states that “In a four bar linkage, the sum of the shortest and longest link lengths should be less than or equal to the sum of the other two link lengths for the linkage to have a complete rotation.”
Four-bar linkages can be classified into different types based on their input-output behavior:
â—Crank-rocker :The input crank can rotate fully while the output rocker oscillates within some limits.
â—Double-rocker :Both input and output rockers oscillate within some limits while one floating link rotates fully.
â—Double-crank :Both input and output cranks rotate fully while one floating link oscillates within some limits.
â—Drag-link :All links rotate fully.
The design of four-bar mechanisms involves finding the optimal dimensions and positions of the links to achieve a desired motion or function. Some methods that can be used for this purpose are:
â—Time ratio :The ratio of the time taken by the output link to move in one direction to the time taken to move in the opposite direction. This can be used to adjust the speed and acceleration of the output link.
â—Timing charts :Graphs that show the angular position, velocity, and acceleration of the input and output links as functions of time. These can be used to analyze the performance and efficiency of the mechanism.
â—Coupler curves :Curves that show the path traced by a point on the floating link or a coupler attached to it. These can be used to generate complex motions or shapes.
Flywheels and fluctuation of energy
A flywheel is a mechanical device that stores energy in the form of rotational kinetic energy. It is essentially a very heavy wheel that takes a lot of force to spin around. It might be a large-diameter wheel with spokes and a very heavy metal rim, or it could be a smaller-diameter cylinder made of something like a carbon-fiber composite.
A flywheel can be used to smooth energy fluctuations and make the energy flow intermittent operating machine more uniform. Flywheels are used in most combustion piston engines. They can also be used as a form of energy storage, where excess energy is stored in the flywheel when it is not needed and released when it is needed.
The amount of energy stored in a flywheel depends on its moment of inertia and its angular velocity. The moment of inertia quantifies the rotational inertia of a rigid body and can be expressed as:
I = k m r2
where
I = moment of inertia (kg m2, lb ft2)
k = inertial constant - depends on the shape of the flywheel
m = mass of flywheel (kg, lbm)
r = radius (m, ft)
The angular velocity is the rate of change of angular position and can be expressed as:
ω = 2 π n
where
ω = angular velocity ( rad /s)
n = rotational speed (revolutions/s, rpm)
The kinetic energy stored in a flywheel can then be expressed as:
Ef = 1/2 I ω2
where
Ef = flywheel kinetic energy (Nm, Joule, ft lb)
The efficiency of a flywheel is the ratio of the output energy to the input energy. It depends on factors such as friction, air resistance, material strength, and shape. Modern flywheels can achieve high efficiencies by using low-friction bearings, vacuum chambers, composite materials, and optimal shapes. A 1977 US Department of Energy pamphlet titled Flywheels: Storing Energy as Motion stated a goal of achieving 70 percent efficiency by 1980.
Power transmission by belts – V-belts and Flat belts
A belt drive is a mechanical system that uses belts and pulleys to transmit power from one device to another. It is a simple and efficient way to transfer rotational power between two shafts that are not collinear (not in a straight line). Belt drives are commonly used in a wide variety of applications, such as in automobiles, conveyor systems, and power transmission systems.
There are two main types of belts used in belt drives: flat belts and v-belts.
Flat belts
A flat belt drive is one wherein the width of the belt is larger than the thickness. These are used where power has to be transmitted for large distances between pulleys. The efficiency of flat belt transmission or flat belt drives is approximately 99%.
Flat belts are produced in the form of long bands and stored in the form of coils. The ends of the belts are joined by any one of the following three methods:
â— Cemented Joints :In this type of joint, leather belts are cemented with a tapered lap joint of length 20 to 25 times belt thickness. Cementing is widely used in rubber and leather belts. The strength of the cemented joint is 80 to 85% of the strength of the belt.
â— Laced Joints :Leasing is done with catgut or with rawhide strips. The strength of the laced joint is 50% of the strength of the belt.
â— Hinged Joints :It takes less time to make the joint and is not suitable for high-speed operations. The strength of the hinged joint is 25% of the strength of the belt.
The amount of power transmitted by a flat belt depends on the following factors:
â— The velocity of the belt
â— Length of the open or crossed belt drives
â— Tension ratio
â— Coefficient of friction
â— Angle of contact
â— Centrifugal tension
â— Creep
V-belts
A v-belt drive is one wherein the cross-section of the belt resembles a letter V. These are used for higher power transmission between parallel shafts having smaller centre distance. The efficiency of v-belt transmission or v-belt drives is approximately 95%.
V-belts are made of rubber or synthetic rubber with fibrous cords embedded for reinforcement. They have trapezoidal cross-sections that fit into matching grooves on the pulleys. The advantages of v-belts over flat belts are:
â— They provide better grip and less slip
â— They can operate on smaller pulley diameters
â— They can withstand higher temperatures and oil contamination
â— They can transmit more power per unit width
â— They can accommodate misalignment and shock loads
The amount of power transmitted by a v-belt depends on the following factors:
â— The velocity of the belt
â— The number and size of belts
â— Tension ratio
â— Coefficient of friction
â— Angle of contact
â— Centrifugal tension
â— Creep
Clutches – Plate and Conical clutch
A clutch is a mechanical device that engages and disengages the power transmission between two rotating shafts. It is used to connect or disconnect the driving and driven members as per the requirement. Clutches are commonly used in automobiles, motorcycles, and machinery.
There are many types of clutches based on their design, operation, and application. Two common types are plate clutch and conical clutch.
Plate clutch
A plate clutch consists of a number of friction plates that are pressed together by springs or hydraulic pressure to transmit torque between two shafts. One shaft is connected to a flywheel that carries a number of driving plates, while the other shaft carries a number of driven plates that are splined to it. When the clutch pedal is pressed, the pressure plate moves away from the flywheel, releasing the friction plates and disengaging the clutch. When the clutch pedal is released, the pressure plate moves towards the flywheel, squeezing the friction plates together and engaging the clutch.
The advantages of plate clutch are:
â— It can transmit high torque
â— It has smooth engagement and disengagement
â— It has low wear and tear
â— It has simple construction and maintenance
The disadvantages of plate clutch are:
â— It requires frequent adjustment of the clutch pedal
â— It has high inertia and heat generation
â— It has limited friction surface area
â— It has high axial force requirement
Conical clutch
A conical clutch consists of two conical surfaces that are pressed together by springs or hydraulic pressure to transmit torque between two shafts. One shaft is connected to a male cone that acts as the driving member, while the other shaft is connected to a female cone that acts as the driven member. When the clutch pedal is pressed, the male cone moves away from the female cone, disengaging the clutch. When the clutch pedal is released, the male cone moves towards the female cone, engaging the clutch.
The advantages of conical clutch are:
â— It has large friction surface area
â— It has low axial force requirement
â— It has self-aligning property
â— It has low inertia and heat generation
The disadvantages of conical clutch are:
â— It has high wear and tear
â— It has jerky engagement and disengagement
â— It has complex construction and maintenance
Gears – Type of gears
Gears are mechanical devices that transmit rotational motion and torque between two shafts by meshing their teeth. Gears can also change the speed, direction, and magnitude of the motion and torque. Gears are widely used in various machines and vehicles for power transmission and control.
There are many types of gears based on their design, operation, and application. Some common types are:
â— Spur gears :The simplest type of gears that have straight teeth parallel to the axis of rotation. They are used for transmitting power between parallel shafts. They have high efficiency and low noise, but they cannot handle high speeds and loads.
â— Helical gears :Gears that have teeth inclined to the axis of rotation. They are used for transmitting power between parallel or slightly skewed shafts. They have higher load capacity and smoother operation than spur gears, but they also produce axial thrust and more noise.
â— Bevel gears :Gears that have teeth on a conical surface. They are used for transmitting power between intersecting or perpendicular shafts. They can change the direction of rotation and the speed ratio. They have different subtypes such as straight bevel gears, spiral bevel gears, and hypoid bevel gears.
â— Worm gears :Gears that consist of a worm (a screw-like gear) and a worm wheel (a helical gear). They are used for transmitting power between non-intersecting and non-parallel shafts. They can provide high speed reduction and high torque multiplication, but they also have low efficiency and high wear.
â— Rack and pinion gears :Gears that consist of a rack (a linear gear) and a pinion (a spur or helical gear). They are used for converting rotational motion into linear motion or vice versa. They can provide precise positioning and movement control, but they also have backlash and wear problems.
CLICK ME TO DOWNLOAD THE COMPLETE NOTES ON MECHANICAL ENGINEERING
No comments added yet!