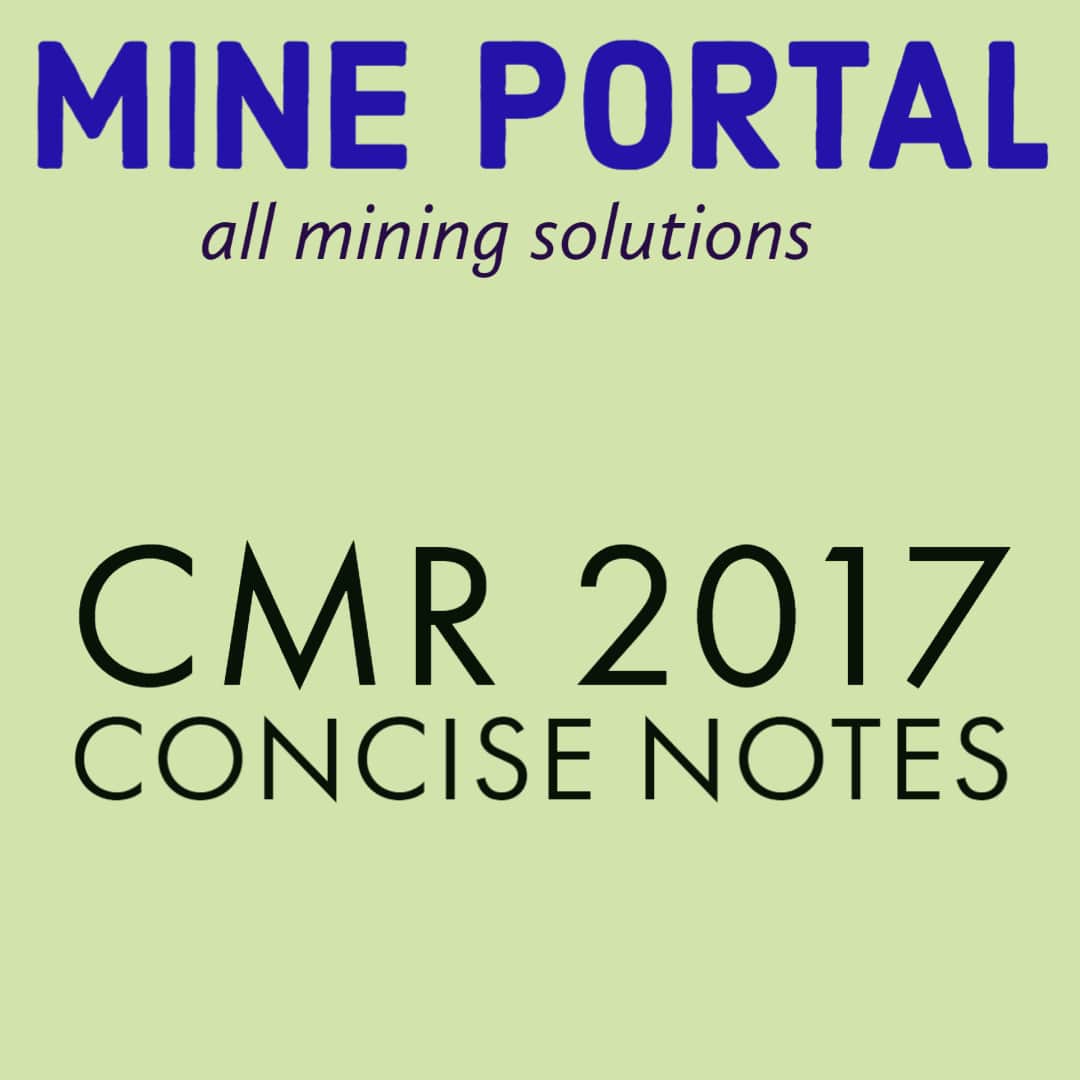
BLASTING IN FIRE AREAS IN OPENCAST MINES
Conditions for conducting blasting in fire areas in an opencast coal mine
(1) Blasting operations shall be carried out under direct supervision of an Assistant manager in charge of Blasting operations.
(2) Persons trained in the job of blasting in Fire area only shall be deputed for the said operation.
(3) No explosive other than slurry or emulsion explosives shall be used.
(4) Blasting shall be done with detonating fuse down the hole.
(5) Temperature inside the blast holes shall be measured (before filling with water) and if the temperature exceeds 80°C, in any hole, such hole shall not be charged. Records of
measurement of temperature in each hole shall be maintained in a bound paged book and shall be signed by the Assistant manager incharge of Blasting operations and
countersigned by manager.
(6) All blast holes shall be kept filled with water. When any hole is traversed by cracks or fissures, such hole shall not be charged unless it is lined with an asbestos pipe and the
hole filled with water. In addition, bentonite or any other effective material shall be used for sealing any cracks at the bottom of the holes.
(7) Detonating fuse shall not be laid on hot ground without taking suitable precautions which will prevent it from coming in contact with hot strata.
(8) Hottest holes shall be loaded last. Uncharged holes shall be filled with water / sandy material.
(9) Carbonaceous material shall not be used for stemming.
(10) The charging and firing of the holes in any one round shall be completed expeditiously and in any case within 02 hours (120 minutes).
(11) Regular monitoring of Carbon Monoxide (CO) shall be done by a competent person authorised by the manager, during charging of the holes. If CO is more than 50 ppm, all
persons from the area shall be withdrawn.
(12) Water spraying / quenching arrangements shall be kept available at the blasting site to deal in case of emergency.
(13) Precautions while drilling in Overburden or Coal over the underground workings in Opencast Mines.
A.Where the underground workings are accessible:
Before commencement of blasting operations in the quarry:
(1) Such workings shall be surveyed and cleaned of coal dust and thickly stone dusted.
All persons shall be withdrawn from the underground in the same working seam or any
other seam or section connected therewith and no work person shall be re-admitted into
the said underground workings unless the same have been inspected by a competent
person duly authorised for the purpose by the manager and found free from any noxious
gases and or signs of fire, etc.
(2) The underground workings to be quarried shall have sufficient thickness of horizontal
barrier as stipulated in the Regulation 121(2) of the Coal Mines Regulations, 2017,
otherwise shall be isolated by explosion proof stoppings such as to withstand the force of
vibration of blasting, from any active working area either in the same or different seam or
section or /mine as the case may be, so as to prevent transfer of danger of blasting to the
said active underground workings.
B. Where the underground workings are not accessible:
Before commencement of blasting operations in the quarry:
Such workings shall be treated with incombustible dust ahead of the quarry face fed through surface boreholes and dispersed by compressed air. The following procedure is
recommended for treating the inaccessible workings underground with stone dust:
(a) Ahead of the bottom bench in overburden, holes shall be drilled 18 metre apart
in grid pattern from top bench in overburden or surface to the underground
galleries. The distance between the 1st row of holes and quarry face should be 06
metre or less.
(b) After holing through of the galleries in coal, the drill rod shall be withdrawn
and at least 02 tonne of stone dust fed through the borehole.
(c) The drill rod shall then be lowered through the borehole again so that it is well
in the heap of stone dust dropped on the floor of the underground galleries.
(d) Compressed air shall then be blown at the rate of not less than 20 m3/min under pressure of at least 3.5 kg/cm² for a minimum of 45 minutes. This time can be
proportionately reduced if compressed air at higher pressure is available.
(e) The steps (b), (c) and (d) shall be repeated with 02 tonne or more of stone dust
dropped in each hole.
(f) If perimeter of galleries exceeds 14 m, the quantity of stone dust dispersed shall
be proportionately increased by repeating the whole process a second time.
(g) For greater effectiveness, the holes shall be drilled in the junctions of the
galleries.
(h) For better dispersibility, it is desirable to use pure limestone dust or dolomite
dust with least possibly silica content. The stone dust should preferably be water proofed in humid and wet conditions.
CLICK ME TO DOWNLOAD THE COMPLETE NOTES ON CONDITIONS FOR BLASTING IN FIRE AREAS
No comments added yet!